Why We Need the Connected Worker
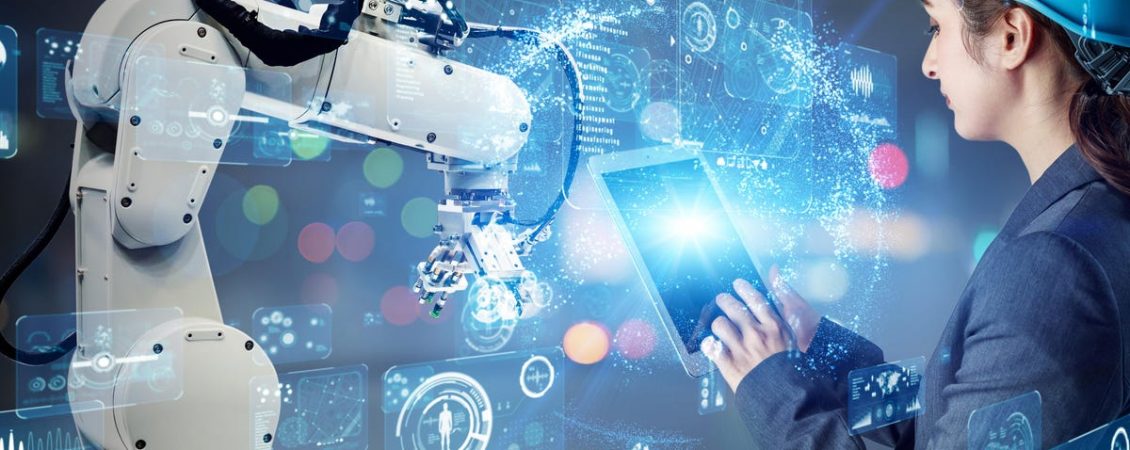
We are currently in the midst of the 4th Industrial Revolution (also known as Industry 4.0, Intelligent Manufacturing or Factory of the Future).
Increasingly, Industry 4.0 technologies are gaining ground in manufacturing – especially during the coronavirus pandemic – and replace paper processes and optimize manufacturing and industrial operations.
However, to keep up with the technological advances of the new era and achieve Operational Excellence (OpEx), it is not enough to invest only in digital machines and platforms. It is also necessary to invest in people – in the connected worker.
The connected worker in industry
Before we explain why the connected worker is essential for manufacturers to adapt to the reality of the market and remain competitive, it is necessary that companies understand the concept behind this worker.
Connected workers, also called augmented workers, are shop floor operators who have a variety of digital technologies, applications and tools – such as a connected worker platform – at their fingertips, keeping them connected to their equipment and to each other.
These technologies are critical to giving these employees a complete, real-time view of operations, as well as the information, services and experiences they need to get their jobs done quickly and efficiently, wherever they are.
Importance of the connected worker
As the coronavirus pandemic has impacted from supply chain systems to the warehouse management, manufacturers around the world are under pressure to bring their factory workforces into the “new digital age” and ensure continuity of their business.
However, Gartner studies say more than 57% of manufacturing leaders say their organization lacks skilled workers to support digitization plans.
Other studies conclude that nearly half of shop floor operators (49%) waste an average of 10 minutes per hour, with the main reason being technology issues such as non-functioning or missing devices. This translates to a loss of productivity of nearly three hours a week per worker.
In this context, the importance of companies training their operators and investing in workers who are connected and familiar with the latest technologies become essential to optimize industrial processes and achieve operational excellence in the digital environment.
Connected factory workers leverage a variety of digital tools and data management techniques to improve and integrate their interactions with the physical and virtual environment, improving decision accuracy, knowledge proliferation and decreasing the chance of errors.
Why should your company invest in connected workers?
Here are some reasons why it’s important for manufacturers to invest in the connected worker and transition their operators to digital and interactive working platforms.
Smart manufacturing depends on technologies and people
As we mentioned earlier, introducing new technologies is not enough to ensure successful operations within Intelligent Manufacturing.
Factory workers must evolve with the technology and be aware of the changes to come. After all, what’s the point of investing in a modern platform with state-of-the-art technology if your employees don’t know how to use it?
We need to make it clear that Industry 4.0 is much more than a digitization process. It requires synchronizing activities through digital tools, but also empowering employees so that there is continuous engagement and learning for better decision making. You need to identify the best starting points for automation and the digital data and tools needed for better decision making. And for that, people are needed. The connected worker is needed.
For example, a connected shop floor worker will know which tool or module to activate in order to automate a repetitive task – such as cutting steel.
In the case of leaders, they will know the way to find management reports and relevant information for decision making.
Again, the importance of professional training in all areas of manufacturing is evident.
The operator is in the center of the shop floor
The shop floor operators know exactly what happens in operations and with the equipment.
As they operate the machinery on a daily basis, these operators – better than anyone else – know what types of information, data and processes can lead to improvements in speed, efficiency or productivity.
However, whether because a plant is still using paper-based systems, or in the context of the coronavirus pandemic – which makes work face-to-face difficult – knowledge about the equipment is rarely shared, which makes it difficult to maintain the processes of production in case an operator retires or is ill.
Let’s go back to the example of the operator who needs to standardize the cutting of steel sheets.
A worker who does not have access to connected tools would likely activate the cutting standardization process and carry out the activity during their shift. But suppose your next shift worker doesn’t know which module was activated to perform a particular cut. This one, of course, will have a hard time accomplishing his task with the same precision and will spend hours finding the way to standardize the cutting of the steel sheets.
On the other hand, a connected worker will be able to inform his colleagues, via digital tools, which module he had activated to cut the sheets and that the path he took to activate that module is the fastest way to automate the task.
Access to information is facilitated
Connected technologies empower operators to make data-driven decisions, improve system-level processes, record incidents and easily share their knowledge with each other. In this way, workers can easily transfer their knowledge from shift to shift and from factory to factory.
Let’s suppose that the worker who had to cut the steel plates needs to record incidents or report technical failures during his shift by making notes on paper to report these events: “There was 15 minutes of machine breakdown”. The operator of the next shift will need to check several notes which, in addition to risking getting lost and compromising the entire operation, will require valuable time.
Studies reveal that the typical worker spends about 20% of their time looking for and gathering information.
Using a digital platform, the connected worker can simply record information and report incidents in real time. This information is instantly available to subsequent shifts as part of a comprehensive knowledge base, overcoming friction and communication challenges that can occur between shifts.
Engaged and satisfied workers produce more
In the context of Industry 4.0, as well as machines and technologies, the human side is fundamental to the success of operations. Therefore, it is very important to motivate shop floor operators so that they work better, maintain product quality and understand their respective importance within the industry.
An excellent option to encourage professional training – especially during the coronavirus quarantine – are digital tools, such as gamification, capable of training employees through games or tasks that can be exchanged for rewards.
At the same time, these tools reduce the time and resources needed to formally train and integrate employees, making the learning process an ongoing activity that newer operators can experience on the machine. And being more autonomous will make workers happier.
It is also worth remembering that, given the pandemic scenario, many manufacturers needed to reduce their shift workforce and migrate to the remote work system.
Thus, the need to invest in workers and connected tools becomes even more urgent for them to be able to carry out virtual follow-up meetings with the team, operate digital tools and perform their tasks remotely via computers and mobile devices.
The connected worker can increase OEE
As a manufacturing strategy, investing in the connected worker has many benefits.
As these operators have all the information that they need to do their jobs in the knowledge base, they can make more accurate and well-informed decisions at any time.
Furthermore, with the help of connected worker platforms, these workers can also increase overall equipment effectiveness (OEE).
OEE is an invaluable production metric and represents how well a manufacturing process is used to its full potential.
This metric combines three factors: availability, quality and performance.
How does the connected worker increase OEE?
Availability
By empowering connected workers to do their jobs independently, manufacturers can reduce equipment breakdown time.
With the aid of a mobile-enabled connected worker platform, these workers can access useful knowledge items on the shop floor and quickly resolve incidents. That same system will also suggest step-by-step solutions and checklists that can save the connected worker valuable time.
It’s also worth remembering that the ability to talk to other colleagues in the same facility or in different factories makes it easier for the connected worker to solve problems.
Performance
Small downtimes and slow cycle times can be difficult to record in paper-based systems.
Using information provided by connected sensors, digital work platforms can detect deviations from a centerline.
From there, supervisors can send notifications to the connected worker to perform a task, such as defect handling or maintenance.
For example, if machines that cut steel sheets experience minor stops, supervisors can send notifications to connected workers to carry out maintenance on these machines.
Upon receiving these notifications, the connected worker will do maintenance on the machine, preventing further downtime that would delay production and compromise equipment performance.
Quality
Achieving the best possible quality is also a critical aspect of operations. Using digital task management tools, connected workers can receive notifications such as scheduling cleaning, inspection and maintenance tasks quickly and easily.
In addition, when a task is due, all relevant workers who are connected to the digital platform will be automatically notified.
Another great advantage of digital platforms is that they store the knowledge shared by workers. Thus, every worker connected to the platform will be able to perform their tasks through step-by-step instructions accompanied by images or video.
For example, the connected worker will be able to use the digital platforms to access a step-by-step checklist on how to activate the correct module to cut the steel plates from our previous example.
This way, the chances of error are reduced and the quality of the parts is not compromised.
Connected workers make it easy to get autonomous maintenance
Since connected workers have digital access to all the relevant data that they need to perform their activities, they can easily perform their own maintenance tasks.
Typically, even in the case of a simple maintenance task, an operator needs to call an engineer or member of the maintenance team, which wastes valuable production time.
With the help of a digital platform, connected workers can perform basic tasks, record, resolve and audit their machines, having greater ownership of their equipment.
This process increases their knowledge of the equipment and free up maintenance staff for more complex tasks. In addition, it improves workers’ ability to identify and correct minor failures before downtime occurs.
How do you take the first steps to make the connected worker part of your manufacturing strategy?
Now that you know why your industry needs connected workers, you may be wondering how to take the first steps to make the connected worker part of your manufacturing strategy.
The first thing to do is to assess the maturity level of Industry 4.0 in your organization to determine and prioritize next steps.
Afterwards, you will need to ensure that your strategy is centered on the operators and their unique work processes in their factories.
So, to truly connect your operators, you’ll need to invest in a complete, intuitive and mobile-enabled connected work platform like Solvace, capable of connecting all your equipment and technologies to your workers on the shop floor.
The Solvace platform helps your company connect workers and achieve Operational Excellence
The Solvace Platform has the broadest coverage in the market to digitize Operational Excellence (OpExc) activities, leading to greater efficiency and effectiveness for the entire industry.
Born on the factory floor, the Solvace platform is modular, with an “all in one” logic, with a single highly efficient and secure database capable of sharing information quickly and easily between front lines and different factories.
The company makes it clear to its customers that despite technological advances and the need for companies to invest in digital to remain competitive, workers are a critical factor for the success of the strategies in Industry 4.0.
In this context, the Solvace platform is designed to combine industry 4.0 technologies with human work, empowering employees and optimizing their operations.
The solution connects all employees and manufacturing locations, generating operational insights and empowering employees at all levels.
The complete set of tools present in the Solvace platform allows to empower employees intuitively and remotely. Reports based on real-time data allow managers to do better.
About Solvace
Solvace is a company that specializes in developing high-performance solutions for manufacturers who believe that Operational Excellence and Digitization are key enablers to improve business results.
For this, we have a team of professionals with extensive expertise on the factory floor, revolutionary software with cutting-edge technologies and the collaboration of leading consultants with OpEx expertise.
Solvace believes that all manufacturing employees should be able to use their platforms as part of a performance management system.
Thus, our main objective is to empower front-line workers with tools that facilitate their work and, at the same time, connect factories from different organizations in a management system that promotes performance and knowledge management.
In the market for six years, partners and customers from different regions of the globe trust Solvace to achieve operational excellence in the digital environment. There are already more than 50 satisfied customers, distributed in more than 75 countries.
Customers range from large global manufacturing companies to local players operating in different sectors such as Services, Consumer Goods, Food & Beverage, Packaging, Process Industry, Automotive, Aerospace, Chemicals and Pharmaceuticals.
At Solvace, each application is developed and customized to meet the needs of each client. Therefore, we work “hand in hand” to find the best solutions and deliver excellent results to our customers.
Contact us and request a free trial.