Top Reasons Why Operational Excellence (OpEx) Initiatives Fail
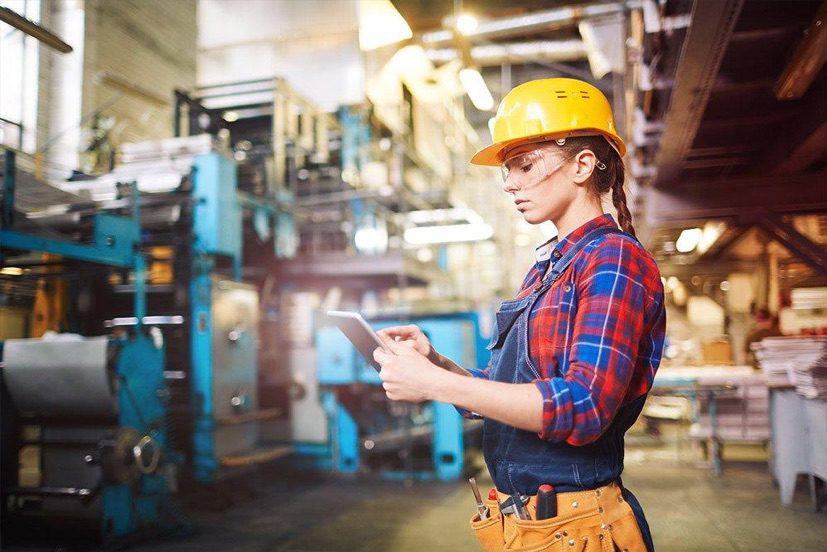
Operational Excellence is a highly popular strategy among businesses and organizations seeking to improve and sustain their efficiency. Despite its growing popularity, it is quite challenging to offer a clear and distinct definition of the domain.
In a nutshell, Operational Excellence is the effort and actions that a company, organization, or institution sets up via standardized processes to push its conviction to deliver towards the client the requested service or product at the requested time and at the smallest production effort/cost and price the client is willing to pay for it.
Surprisingly, many organizations continue to struggle with Operational Excellence. There are times when OpEx fails to deliver the desired results. Notably, it is possible to determine what caused the failure of the OpEX process.
Knowing the reasons that caused the failure of your OpEx and keeping them in context along the way has enabled many users to devise strategies for ensuring that they achieve the desired results in their OpEx projects.
Why Operational Excellence Fails
Company leaders do not have adequate information and knowledge about Operational Excellence, and they begin using OpEx for the wrong reasons.
There are times when companies launch OpEx initiatives since else “everyone is doing it” or maybe because competitors invest in Operational Excellence. Furthermore, the local branches of a firm are frequently compelled to begin with Operational Excellence because the company’s headquarters has decided that is the way things must be done.
In these circumstances, most organizations lack the necessary knowledge, expertise, manpower, and funding to begin and achieve optimal results with OpEx.
Experts advise that companies should only begin with Operational Excellence if they are confident that OpEx will provide significant benefits. Also, only invest in OpEx if you have the necessary knowledge, expertise, and resources available to implement the project and integrate it into your company’s operations.
If you’re not sure if you’re ready or if Operational Excellence is right for you, Solvace is here to help. Inadequate knowledge, expertise, or lack of resources should never be an impediment to optimizing processes.
OpEx is viewed as a set of tools rather than a culture
If you believe that implementing a small or large program will provide you with Operational Excellence, you are mistaken. Operational Excellence is part of a philosophy, and a company culture. For anyone who wants to reap the benefits of OpEx, they will need to implement more than a few methodologies.
A functional model required to lead the cultural changes that come with the implementation of OpEx programs. The entire organization must be on board for the program to be successful. Operational Excellence comes with many benefits to the organization.
Not enough people have the right soft skills to help with cultural change
The majority of businesses believe that having just a few skilled and knowledgeable employees on staff is sufficient to support the implementation of successful OpEx programs. In the real world, however, this is not the case.The implementation and success of Operational Excellence initiatives do not have to rely on a small group of individuals with the necessary soft skills and expertise.
These OpEx initiatives must originate with and be accepted by everyone in the organization regardless of their skills, education, expertise, and position within the organization. Hence, OpEx requires more than a few individuals with the right expertise and soft skills to succeed. Working on an Operational Excellence project requires a collaborative effort. To achieve the desired results, the entire organization must be supportive.
Operational Excellence is implemented top-bottom, no attention is given to bottom-up feedback
Many of these companies and organizations implement OpEx in a top-down manner. Nonetheless, the projects fail due to a lack of participation from many employees. This occurs because, in many cases the organizations pay little to no attention to the feedback that comes from the shopfloor.
In these cases, the workers and first-line management can quickly shift from a cooperative “Plan Do Check Act” mentality to a passive “I’ll only do what they tell me” mentality in these situations.
Because Operational Excellence requires the entire team to succeed, it is critical to pay close attention to feedback from all parties involved. For the OpEx project to succeed, everyone must be on board and stay on board throughout.
Leaders are not required to implement all of the feedback they receive. However, they must create an environment in which people feel understood and heard. From there, they can then work on the best feedback to increase the success of the implemented OpEx initiative. Solvace can help in creating an Operational Excellence model that incorporates everyone and ensures that their opinions are understood.
OpEx is rolled out as a single approach for everyone
Each machine, colleague, department, production line, and process has unique characteristics. It is never a good idea to ‘generalize’ the implementation of Operational Excellence strategies in this context. Some departments and individuals may prefer a big bang strategy, whereas others prefer a step-by-step approach.
Others on the other hand, will prefer a process-oriented or a department-oriented approach. Thus, forcing a single approach on everyone is almost always a recipe for disaster.
In that case, experts advise that organizations need to find stratergy that resonates with most people, departments, processes, and working environments. They can use different approaches for different groups using the right tools for the right individuals at the right time.
Too many changes within a short time frame
Most organizations that invest in and implement Operational Excellence are looking for quick fast results. In that context, they typically initiate many changes within a short period of time. People in these scenarios absorb, understand, accept, and implement the changes correctly before the next set of changes are introduced.
As a result, errors, instability, and safety risks become a possibility. It eventually leads to a lower levels of results which may be detrimental for the organization. Thus, top executives and business owners need to take their time while implementing OpEx initiatives. Before any major changes are implemented, they must ensure that all initiatives are understood, accepted, and practiced.
Shopfloor managers fail to show adequate involvement
Shopfloor managers are responsible for ensuring that the production and services keep running smoothly in order to improve results and profit margins. However, due to the rapid changes occurring in the world, figurative firefighting has become the “general modus operandi” these days.
When the shopfloor managers are busy fixing problems, they are not much interested in implementing new Operational Excellence initiatives. When such situations arise, the line managers fail to provide the support and motivation that is necessary to inspire other members of the shop floor.
Hence, before implementing any OpEx initiatives, always ensure that the manufacturing managers are not preoccupied with other matters. You will not achieve the desired results if they do not join in.
Losing sight of the customer
Many businesses and organizations exist because of their loyal customers. The customers pay for goods and services. Thus, if a company sets its prices too high, perhaps as a result of inefficient processes and poor Operational Excellence, it will go out of business as customers will go to competitors.
Thus, companies must constantly look for ways to improve their OpEx in order to improve their position in the overall market and command a considerable market share. To improve, always ask the question “Does the customer want to pay for this?”
Thinking that OpEx is a one-off thing
Companies and organizations implement a variety of OpEx tools and methodologies and then use the implementation date to determine the end date of their OpEx process. However, Operational Excellence is a never-ending process. o be truly successful, everyone in the company must constantly question how things are done and how they can be done more efficiently and effectively.
Operational Excellence is a never-ending story. Companies must take the time to challenge the status quo if they are to succeed. Those who expect good results from their OpEx initiatives must maintain continuity.
Solvace Advice On How To Make Operational Excellence Initiatives Successful
Companies must avoid the discussed pitfalls to ensure that their Operational Excellence programs prove successful. Furthermore, Solvace advises that companies need to be well-prepared before implementing OpEx initiatives and that the programs should be implemented for the right reasons.
Sufficient knowledge, expertise, and soft skills are required to ensure the success of all the initiatives implemented. Notably, leaders and top executives must leave some room for people to adapt to the new ways and embrace the necessary changes in the company’s culture.
Leaders can also achieve success by listening to all feedback from those involved and then tailoring their implementation strategies to the individuals, departments, and processes involved in the initiative.
Always use the right processes to improve customer experiences and make sure that the investment in Operational Excellence projects is ongoing. Shopfloor managers must be able to motivate and inspire their coworkers. These initiatives must also be implemented in a sequential manner to ensure that all participants understand what they entail to guarantee optimal productivity is achieved.