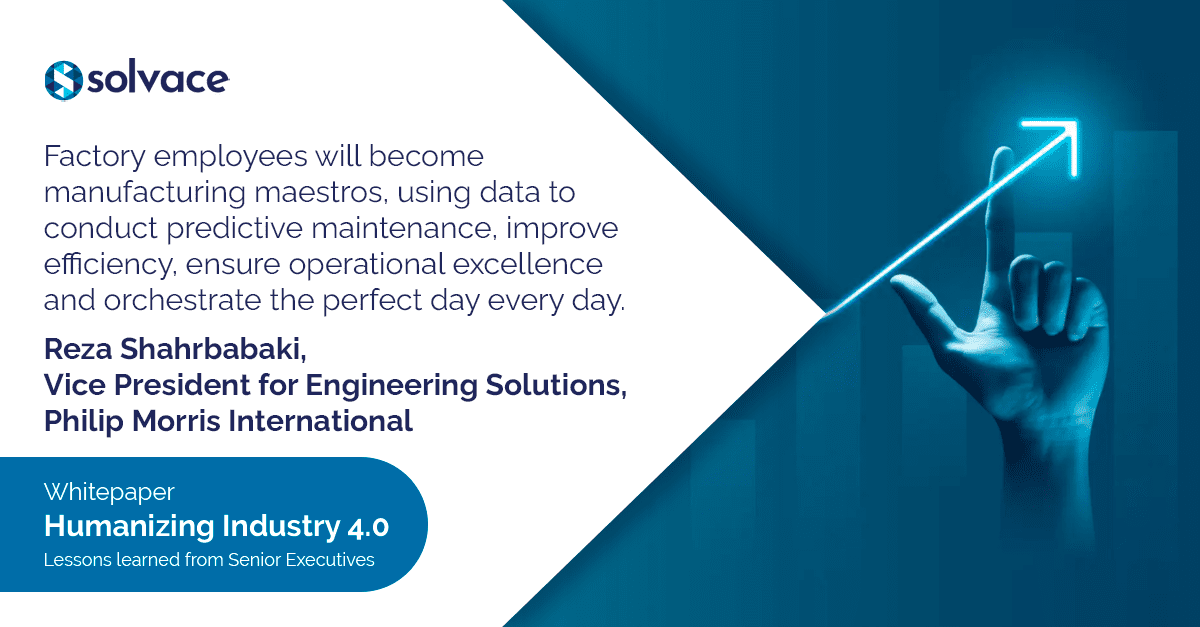
Philip Morris – Orchestrating the Perfect Day
“Factory employees will become manufacturing maestros, using data to conduct predictive maintenance, improve efficiency, ensure operational excellence and orchestrate the perfect day every day.”
Reza Shahrbabaki,
Vice President for Engineering Solutions, Philip Morris International
Orchestrating the Perfect Day
There’s an ambition in manufacturing: A perfect day on the production floor where there are no safety nor quality incidents, and when there are no unplanned stops on the machines. It’s PMI’s ambition and what they’re striving for as part of their lean manufacturing methodology – having the right set of tools, processes and capabilities to make every day a perfect day.
According to Reza Shahrbabaki, Vice President for Engineering Solutions at Philip Morris International (PMI), the perfect day is no longer a factory fantasy. With the right data, processes and mindset it can be a reality.
If you analyze the data from what happened on even a near-perfect day, you can better understand the critical values and variables that were in play” he says. “If you understand this, you can replicate it, essentially creating a digital twin to the perfect day.”
Unfortunately, doing this is easier said than done. That’s because digitization is a journey that takes both patience and resources. “Just as Rome wasn’t built in a day, neither is the perfect day” adds Shahrbabaki. “In other words, you cannot launch something of this magnitude and expect to see results in six months – change takes time.”
_________________________________________________________________________
Back to Basic
While there may not be a shortcut to achieving the perfect day, companies do have access to ‘enablers’ – a sequence of steps, with each step enabling the next. One of the first steps in the company’s digitization journey was to become more like an ATM machine.
“Many of us across the world use ATM machines. Over the years these machines have standardized the human machine interface (HMI) and we have reached the stage where you can close your eyes and go through the procedure as you know the sequence by heart. The question I have is : ‘Why should the HMI in manufacturing systems be so complicated ? We should have this same level of user friendliness with our machines so operators, no matter where they are located or what machine they are using, will intuitively know what to do” says Shahrbabaki.
For Shahrbabaki, this exemplifies the importance of getting the basics right. “A digital transformation must start with the basics – ensuring you can access the data you do have and then use it in your operations on a daily basis” he adds.
_________________________________________________________________________
People-Powered
Digital transformation isn’t just about technology; it’s powered by people. It’s like a symphony orchestra – you will get harmony while working together only when everyone plays their part best and listens to others.
When teams collaborate, silos disappear, and businesses can adapt faster. Being on the ground, in the ‘gemba,’ encourages us to dream big but start small, test ideas, embrace successful strategies, and continually improve. Think of it like building a skyscraper, one floor at a time, ensuring each level is sturdy and well-crafted.
Open communication and a focus on customers becomes the guiding star, where data and technology are trusty tools in our hands, used by our people who make the magic happen in the digital world!
_________________________________________________________________________
“There is no finish line to digitization, it’s an ongoing process – and challenge.”
says Shahrbabaki.
Towards the Factory of the Future
Thanks to its step-by-step approach to digital transformation, PMI continues to make its manufacturing processes smarter.
Having put in the time to get the basics right, the company is well positioned to evolve into the next phase of its digital transformation, a phase that Shahrbabaki believes will involve even smarter machines and more data, reducing repetitive or ergonomically unsuitable tasks.
_________________________________________________________________________
Manufacturing Maestros
But this doesn’t mean humans will be replaced – far from it. According to Shahrbabaki, tomorrow’s factory will be like today’s air traffic control tower. Instead of pushing buttons and restarting machines, factories will have highly skilled workers monitoring and managing operations from data-driven control rooms. And just as components of an aircraft communicate directly with a control tower, the smart machines of the future will communicate directly with the workers in the control room.
Factory workers will become manufacturing maestros, using data to conduct predictive maintenance, improve efficiency, ensure operational excellence and orchestrate the perfect day every day.
concludes Shahrbabaki.
_________________________________________________________________________
Want to know more?
Whether you have any questions or need more info, we would be happy to help!
“Regardless of how digital a company becomes, you cannot remove the human factor.”
Kyle Tansill,
Digital Manufacturing Solutions Architect, Saint-Gobain Performance Plastics
Revolution 4.0
At Saint-Gobain, which designs, manufactures and distributes materials and services for the construction and industrial markets, the Industry 4.0 revolution is just as much about people as it is about digital.
2018. That was the year the revolution started. “There was a lot of hype but also a lot of confusion” recalls Kyle Tansill who, as an automation engineer, was on the frontlines of Saint-Gobain’s Industry 4.0 revolution.
According to Tansill, who today serves as Digital Manufacturing Solutions Architect at Saint-Gobain Life Sciences, the spark that lit the digitalization fire was a spur of acquisitions. “Facing a low level of standardization for our machinery, we turned our focus to automation and connectivity” he says.
It was also a matter of bringing the company from the Paper Age into the Digital Age. “We got to work using Google Maps on our smartphone, but once we are there, we switch the phone for pen and paper,” explains Tansill.
However, as Tansill is quick to point out, the solution to this problem wasn’t as easy as replacing the pen and paper with tech and apps. Change is never so simple. “We brought in all these sexy tools and then we realized that while everyone knew we should be doing something with them, nobody actually knew what that something was,” he adds.
_________________________________________________________________________
Bridge a Disconnect
To bridge this digital disconnect, the company took a couple of steps back. They started with skills, ensuring that its people had basic automation skills. They also upgraded their PLCs and invested in automation infrastructure.
As a result, today Saint-Gobain is in a position where most of its strategic machinery features updated PLCs and some form of connectivity. Most importantly, its sites are staffed with people who understand automation.
“Our teams didn’t know what an industrial network was just a few years back” remarks Tansill. “Since then, they’ve developed the necessary skills, which puts us in a really strong position going forward.”
_________________________________________________________________________
Digitize Your Head
While going forward does mean increasing automation, it does not mean replacing people. “Regardless of how digital a company becomes, you cannot replace the human factor,” says Tansill.
So, how does one preserve that essential people component in a sector notorious for having a high turnover?
Somewhat ironically, the answer is digitalization.
“Turnover means more than just having to train new people, it also means constantly losing your company’s knowledge base” explains Tansill.
To help plug this leak, Saint-Gobain is in the process of digitizing its know- how. One approach being implemented involves utilizing data to establish standardized operating procedures for its machinery. This ensures that the operational steps are embedded within the machine itself, rather than relying on an individual’s memory or personal knowledge.
The company also decided to bring in a ringer. “We employed a top-level senior software engineer who was an incredibly talented Python developer and all-around software genius,” says Tansill.
_________________________________________________________________________
“I don’t even like the term Industry 4.0, believing it gives the false perception that one comes in, does digital, and then is done.”
Achieving the Goal of Performance
While the developer was only with the company for less than two years, his impact remains. “Having this developer allowed our automation developers to learn how to develop properly and then implement a proper continuous integration lifecycle and support system” adds Tansill.
We’d All Love to See the Plan
Over the course of six years, Saint-Gobain went from Industry 3.0 to Industry 4.0. Yet its journey is far from over. In fact, Tansill doesn’t even like the term Industry 4.0, believing it gives the false perception that one comes in, does digital, and then is done – which clearly is not the case.
“Digital shouldn’t be seen as the end but the means to achieving the goal of improved performance” says Tansill. “Whatever domain you’re working in, you need to accept that even though your expertise might be digital, you are just as responsible as everyone else for the company’s performance.”
Yet while Saint-Gobain’s digital transformation may be an ongoing work- in-progress, they do have the benefit of hindsight – meaning they can offer some sage advice for those just starting off on their journey.
_________________________________________________________________________
Having a Clear Plan is Key
“Do not start this journey without a clear plan of where the business is going” warns Tansill.
As Tansill explains, without a plan, you risk deploying technology for technology’s sake. “But with a well thought out roadmap, you can match technology to objective, ensuring that every investment gets results, improves performance and, ultimately, advances the company towards where it wants to be” he concludes.
_________________________________________________________________________
Want to know more?
Whether you have any questions or need more info, we would be happy to help!