Industry 4.0: Best Practices and How to Implement a Good Strategy
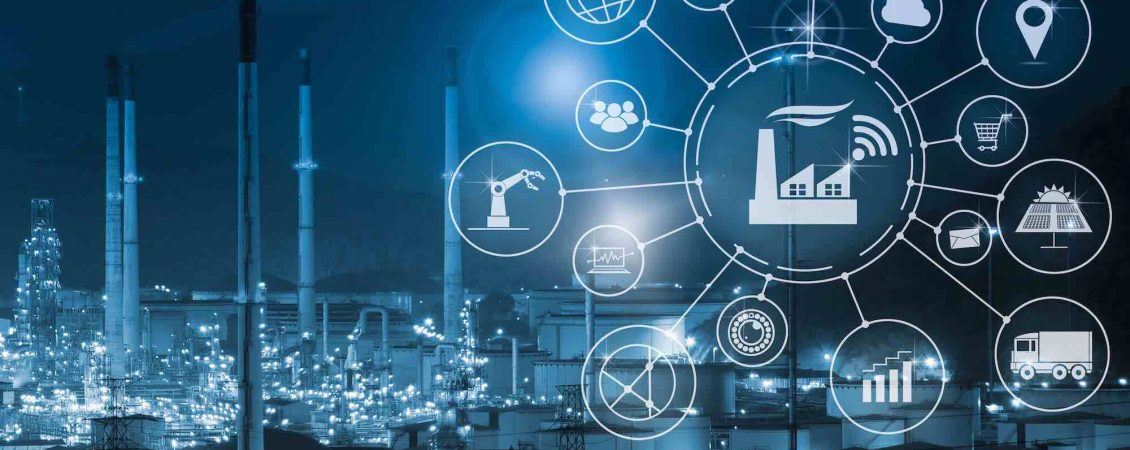
We live in an era of constant transformations in the production chain and in the way of doing business. In industry 4.0, the so-called Factory of the Future is already a reality. Technological advances and digitization are gaining more and more space and human labor is combined with intelligent and disruptive technologies.
It is up to companies, then, to rethink their strategies and adapt to the “new” Industry to survive the competitive market.
What is Industry 4.0?
Industry 4.0 is the term used to refer to the Fourth Industrial Revolution. It is a new era where connectivity, automation and digitization technology are used to optimize manufacturing and industrial processes.
Its great differential is the digitalization of physical assets, with sensors incorporated in practically all equipment. This digitization allows for full integration of the entire factory.
Therefore, it is no longer about automating a single process, or investing in technologies to solve a specific problem. In Industry 4.0, the physical and the virtual come together completely so that everything can be measured, analyzed and optimized.
It must be made clear, therefore, that the concept involves the entire value chain of the industry, not just the production and distribution processes.
Technology Trends and the 4th Industrial Revolution (Industry 4.0)
Leaders in technological and industrial innovation acknowledge that Industry 4.0 is comprised of key trends. Let us deep dive into 9 of them, considered by some the foundation of Industry 4.0.
According to some studies, many of these trends are already used in manufacturing and they will transform production.
Isolated and optimized cells will integrate into a single automated flow, resulting in greater efficiencies and changes in traditional relationships between producers, suppliers and customers – as well as between machine and human.
Big Data and Analytics
The use of Big Data and Analytics is new in the manufacturing world.
These tools are responsible for collecting and analyzing large sets of data. Thus, from the information obtained, it is possible to optimize production quality, save energy, identify failures at the beginning of the production process and, consequently, improve the performance of equipment and production quality.
In the context of Industry 4.0, data-based analysis encompasses the collection and evaluation of information from different sources. Examples are: production equipment and systems, and corporate and customer management systems. This data, in turn, is critical to support real-time decision making.
Smart robots
The use of intelligent robots in the most diverse sectors of the industry is nothing new.
For some years now, these robots have been used to perform complex tasks. However, with technological advances, they are evolving to become more autonomous, flexible and cooperative.
Eventually, intelligent robots will interact with each other as well as humans, learning and working safely and attuned. In addition, the cost of these robots will be lower and will have a greater range of features when compared to those used in factories today.
Integration between horizontal and vertical systems
Currently, most Information Technology systems in companies are not fully integrated.
Different departments in the company rarely communicate, and even company functions at the shop floor level are not fully integrated. Even engineering itself – from products to factories and automation – lacks complete integration. Furthermore, companies, suppliers and customers are rarely closely linked.
However, with the implementation of Industry 4.0 technologies, companies, departments, functions and resources will become more cohesive as data integration networks evolve and enable truly automated value chains.
Industrial Internet of Things
Currently, not all sensors and machines from manufacturers are networked and make use of embedded computing. They are typically organized into vertical automation pyramids, where sensors and field devices with limited intelligence and automation controllers feed into a comprehensive manufacturing process control system.
However, with the implementation of the Industrial Internet of Things, more devices and even unfinished products will be enriched with embedded computing and connected through standard technologies.
In this way, field devices will be able to communicate and interact with each other and with more centralized controllers as needed. It will also be possible to decentralize analysis and decision-making, enabling real-time responses.
Simulation
Currently, the engineering sector already makes use of 3D simulations of products, materials and production processes.
In the future, however, these simulations will also be used in factory operations. These simulations will be able to leverage real-time data to mirror the physical world in a virtual model, which could include machines, products and humans.
Operators will be able to test and optimize machine configurations for the next product in the line in the virtual world before the final release in the physical world, thus reducing machine setup times and increasing production quality.
Augmented Reality
Augmented reality-based systems support a variety of services. Examples are: selecting parts from warehouses and sending repair instructions via mobile devices.
In the future, these systems could provide companies with real-time information to improve decision making and streamline operations. Workers will be able to receive repair instructions on how to replace a part, while looking at the actual system that needs repair, for example. Such information can be displayed directly in the field of vision of workers through devices such as augmented reality glasses.
Another application is virtual training. Through augmented reality systems, it will be possible to create software that uses realistic 3D environments based on data to train teams for emergency situations. In the virtual world, operators will be able to learn to interact with machines and will be able to change parameters to retrieve operational data and maintenance instructions.
Additive Manufacturing
Initially, additive manufacturing, such as 3D printing, was implemented in companies to create prototypes and to produce individual components.
Through Industry 4.0, additive manufacturing methods will be widely used in the production of small batches of customized products, offering construction advantages such as complex and lightweight designs.
In addition, these systems will be decentralized and high-performance, reducing transport distances and available inventory. Consequently, expenses with raw materials and the weight of transport will also be reduced, making operations cheaper.
Study data estimates that the cost savings that can be achieved with Industry 4.0 transformations is 50%.
Cloud
Most companies already use cloud-based software for business and analytical applications.
However, with Industry 4.0, more production-related ventures will require greater data sharing across company locations and boundaries. At the same time, the performance of cloud technologies will be improved, achieving reaction times of just a few milliseconds.
As a result, the functionality of the machines and the data generated will be increasingly stored in the cloud. This storage will allow sensitive information to be stored more securely, as well as allowing more production systems to be data-based. Even systems that monitor and control processes could become cloud-based.
Cybersecurity
With the increase in connectivity and the use of standard communication protocols, the industries of the future will need to invest in industrial systems and software capable of mitigating the risks of information leakage and threats to digital security.
Therefore, secure and reliable communications, as well as training staff to handle sensitive data and manage access to information will be critical.
Industry 4.0 Benefits
Bringing Industry 4.0 technologies into factories is not always cheap. However, there are significant advantages for companies to adopt the latest in the industry.
Better use of resources
The adoption of the Lean Manufacturing concept is nothing new in companies. However, there are those who argue that only now can it be effectively put into practice.
It is a methodology that defends the idea of eliminating any type of waste to increase productivity and optimize processes. The idea, therefore, is to make the most of available resources (people, machines, equipment, raw materials, etc.).
In addition, Industry 4.0 technologies generate a high volume of data, which allows the application of continuous improvement processes in search of an almost perfect optimization.
Operational cost reduction
Studies by ABI Research and Ericsson estimate that mobile-enabled Industry 4.0 solutions can generate operating cost savings of 10 to 20 times ROI (return on investment) over five years.
In addition, the same survey suggests that Industry 4.0 solutions can generate operating cost savings of up to 8.5%. For a factory or industrial site, this amount can equate to operating cost savings of up to $600 per square foot per year.
Agility
Adapted to technologies that allow them to perform actions in seconds, consumers are increasingly demanding and immediate.
In this context, the speed of the production line is one of the factors that can influence the purchase decision and the consumer experience.
According to the “Deliver the CX They Expect: Customer Experience Trends” report, only 10% of consumers believe brands meet their customer experience (CX) expectations.
Therefore, in an era of extreme immediacy where the focus is on the consumer, companies that invest in technologies capable of reducing production time without increasing costs or losing the quality of the final product come out ahead.
Risk reduction
The human factor is crucial in Industry 4.0. The manufacturing sector usually suffers a lot from accidents, indemnities and labor lawsuits.
In this context, technology can be a great differential to prevent these types of problems.
Through the analysis of data and reports generated in real time, it is possible to improve machine maintenance management and have greater control over the activities performed by employees.
Expectations for Industry 4.0
MarketsandMarkets projections estimate the Industry 4.0 market to reach $156.6 billion by 2024, at a compound annual growth rate (CAGR) of 16.9% from 2019 to 2024.
According to this survey, the factors behind such theory are technology trends, such as leveraging the Internet of Things (IoT), including wireless networks and sensors for machine data collection and predictive maintenance permits, as well as 3D printing, robots smarts on the factory floor, machine learning and Artificial Intelligence (AI), 5G and digital twins, among others.
The same survey further concluded that, based on technology trends, the IoT segment will be the biggest contributor to Industry 4.0 growth over the forecast period. The study concluded that the potential benefits of the segment encouraged several industrial equipment manufacturers to implement it. However, the ability to remotely monitor corporate assets and perform predictive maintenance is the main reason for its growing adoption.
Industrial robotics are also expected to be the 2nd largest contributor to Industry 4.0 growth. According to the study, manufacturers are turning to automation in response to the growing shortage of skilled workers in the manufacturing sector. Furthermore, the price of industrial robots has dropped in recent years and has become much easier to program. In response to this lack of skill, the trend is for industrial robotics to increase, particularly in developed countries.
How to implement Industry 4.0 technologies in business?
Advanced manufacturing companies are implementing new technologies such as AI, IoT, data and analytics to drive growth and profitability.
To ensure success, industry leaders must go beyond the hype of new technologies and develop future-ready strategies to manage change and capitalize on opportunity.
Create a strategic plan
Introducing Industry 4.0 concepts requires planning.
Thus, the first thing to be done is to understand what are the main problems faced by the company and what are the best technologies that can be adopted to, little by little, solve these problems.
Currently, there are several solutions on the market. However, factories should only bet on those that can provide them with a high ROI based on the main short-term pains.
Conduct a technology assessment
Industry 4.0 will completely change the technological nature and IT ecosystems of factories. However, this change will depend, in large part, on what this ecosystem already looks like.
Therefore, in parallel with the strategic plan, it is necessary to audit the technology already used by the company. This audit should include everything from implemented software (APS or S & OP systems, for example), as well as any physical hardware such as servers, computers and even shop floor machines.
The technology audit will be able to give an overview of how far a company’s digitization efforts are or how well positioned a business is for further technology integration.
If, for example, the company is operating with a lot of modern computer hardware to store production data and customer orders, the business is likely to be in a position where new technologies can access this data without much effort. On the other hand, if the company is still operating with old servers without a network connection, it will need new technologies to adapt to the new market reality.
Invest in pilot projects
As attractive as it is to experience the news of the new industrial revolution, leaders must have their feet on the ground.
As they are high cost technologies, most technology companies that offer solutions for Industry 4.0 allow pilot projects to be carried out. Take the opportunity to start small, run tests and analyze the first results.
If all goes well, don’t be afraid to invest and expand the project to other areas of the company.
Bet on connectivity
While there are many variations in how technology deployment evolves depending on your organization’s exact needs, there is one element of Industry 4.0 that should not be negotiable: increased connectivity across the entire value chain.
As it becomes critical to understand the management capabilities of existing devices in the enterprise, you also need to examine and understand how IoT device management systems connect to your facility’s enterprise management system (EMS).
The EMS is responsible for overseeing the installation as a whole and controlling how various systems operate and interact. As such, it is essential that it communicates effectively with device management systems so that operations can run effectively.
Don’t neglect advanced analytics
Just as connectivity is non-negotiable, it is also critical that companies invest in solutions capable of extracting relevant data – whether in machine learning-derived forecasting, real-time traffic and price analysis or automatic network optimizations.
This analysis is critically important, as the more technologies that are implemented in operations and the more they integrate with supplier and customer IT, the more data operations will produce.
While much of this data may appear opaque to a human planner, advanced analytic workflows can ensure that this data translates into real value in the form of better forecasts and reduced waste.
Prioritize cloud-based deployment options
Cloud computing allows storing more information in highly secure databases and is a trend for the next few years.
Additionally, most Industry 4.0 technologies have cloud deployment options.
The more manufacturers learn about cloud-based deployment options and how they work with their Industry 4.0 systems and processes, the more likely they are to find the right deployment options for their operations.
Prepare teams for Industry 4.0
No technology will bring good results if there is not a qualified team to operate it.
Therefore, industry 4.0 professionals need to reinvent themselves. It will be increasingly necessary to have analytical and data interpretation skills.
In addition, you need a team that adapts easily and learns quickly, as innovations are constantly changing and there is always something new in the market.
How can Solvace help you with your digital journey in OpExc in Industry 4.0?
If your company wants to empower frontline workers with tools to make their job easier but at the same time connecting plants and different organizations in a management system that promotes performance and knowledge management. Industry 4.0 is all about merging technology, process and people. Solvace is the right partner for your digital journey in OpExc!
Contact us and request a demo.