How to Improve Operations in Manufacturing
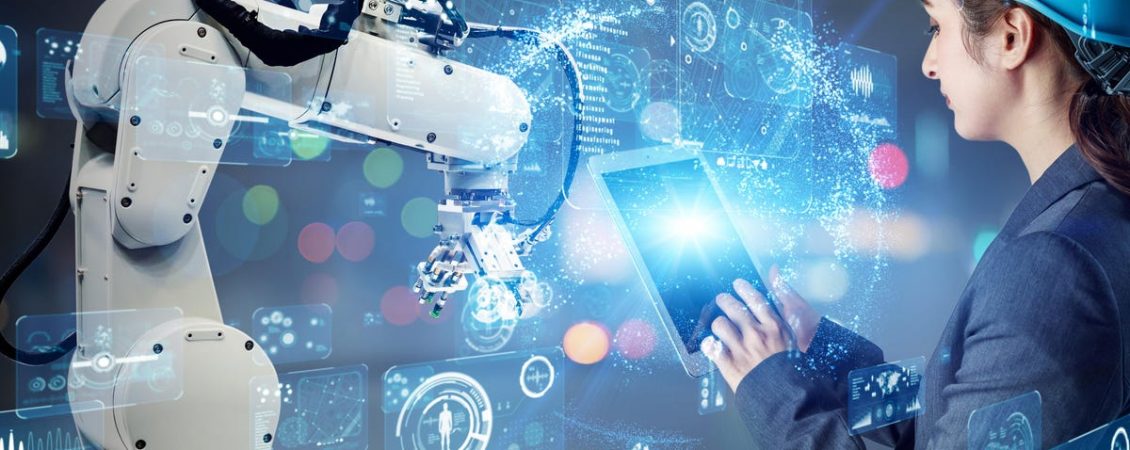
Improving operations in manufacturing seems to be at the top of the list of every management team.
Getting the most out of your equipment, processes, and personnel is a time and effort investment that is worth what you put into it. Whenever you are ready to improve operational efficiency at your facility, you can follow the advice given by the Solvace experts to start on the right foot.
It is quite challenging for anyone trying to improve operations in manufacturing. Challenges and pressures are enhanced by having to work to tight deadlines and, as a result, the productivity of both onsite and offsite employees can be impacted by the availability of time-critical information.
Adding business activity monitoring system automation and integration capabilities to manufacturing software solutions enables manufacturers to become lean and highly profitable by automating the back office operations that cost significant amounts of time and money.
Here are ways to improve operations in manufacturing:
Automate Processes
Automating processes means that the service managers no longer need to spend time on repetitive duties. Instead, they can devote time to their work closely with their clients.
Business process automation enables reports to be generated and distributed automatically to offer an instant, positive impact in real-time, hence reducing reconciliation times.
Moreover, various dashboards are mostly used to display an overview of real-time information that can be accessed rapidly and ready to help in decision-making. For instance, finance and accounting professionals can view a summary of financial transactions and statuses, whilst stock management teams can view stock levels, values, and gradual moving stock to help procurement and production processes.
It is always advisable to update your automation practices and systems for optimal performance. Automation has been proven to be one of the most reliable and effective ways to improve operations in manufacturing. The current systems are using technology and data to be ‘smarter’ and more efficient than ever.
Whether you are replacing controllers or components, integrating automation with “old-iron” equipment, or installing extra technology to be more collaborative with the human workers, reviewing the current automation in your firm and identifying the available opportunities is a perfect place to start to enhance operational performance.
Dynamic Stock Management
Stock management is a continuous activity for manufacturing organizations. Being dynamically informed when the stock levels drop below agreed levels offers the stock controllers some detailed reports on sales orders placed on the system that can assist in pushing fulfillment stock levels into negative territory. That enables the business to respond rapidly to getting products on the production plan for the manufacture or purchasing of new materials.
Real-time Data For The Sales Team
The availability of real-time information is crucial to all sales forces. Without any real-time information, existing clients can suffer from poor service and sales representatives may miss out on various sales opportunities.
Manually developing and distributing the sales reports to field-based sales teams is an efficient use of the employees’ time and an extra cost that can be smoothened and eliminated. In most cases, a manual report creation process can result in out-of-date information that is not quite relevant to a sales team after the report gets distributed.
Automation of reports offers sales teams real-time sales information that is automatically identified, formatted, and then distributed without any employee intervention –error-free. Real-time sales reports can include daily sales orders, customer turnover, invoices processed today, or orders waiting to be dispatched; all relevant information for a field-based sales representative.
Keep The Manufacturing Plant Safe
It is quite important to boost security in your production area. Manufacturing operations feature the use of heavy machines and equipment that have high accident risks.
When a worker is injured on the production floor, all processes have to stop instantly. Such incidents cause product delays meaning that you may need to reschedule the entire production process once more.
Other challenges that may come up from the lack of security on factory floors include loss of efficient and skilled workers, increased insurance costs, production floor closures for incident investigation, damage to the production equipment, and much more. Hence, it is advisable to prioritize workplace safety to enable employees to work optimally without having to worry about injuries.
Safety is a major responsibility of workers. It plays an integral role in an efficient facility. Injuries and equipment malfunction need downtime, in some cases for the whole facility, and will normally need equipment repairs, time off, maintenance, and many other resources in reviewing and correcting what went wrong. Maintaining a company-wide focus on safety helps in avoiding these issues.
Keep Up With Maintenance
Any improperly maintained machines undermine efficiency in manufacturing processes. Neglected machines break down regularly, do not operate at peak performance, and can pose dangers to workers. Consider adhering to a preventive maintenance schedule, instead of a reactive approach.
Operations in manufacturing can also be enhanced via predictive maintenance practices that utilize equipment performance data to determine possible issues early on, resulting in a more targeted and effective maintenance practice in your company.
Train And Retrain
Employee training covers a wide range of areas including safety, company-specific information, best practices and much more. The famous saying goes, “knowledge is power,” and in a manufacturing company, it is believed to be true.
Ensure that all employees have been trained recently and updated in best practices for machine maintenance, operation, and safety; as well as all other areas that are pertinent to your operation.
Review Factory Floor Layout
For the related processes to function together efficiently, the factory floor needs to be laid out in a scheduled and intentional way. In case you have extra equipment and capabilities over the years, the floor layout may not be optimized, and you may not be operating as efficiently as you can.
Assess your processes, current layout, and workflows, then determine whether various locations for equipment might be worth the time investment.
Define Goals
With an efficiency goal, all employees can have a solid target to work toward. Benchmark the current efficiency performance metrics, including accepted pieces per cycle, cost per part, average downtime, relevant failure metrics, and overall equipment effectiveness (OEE).
You can then decide how you want to see these numbers improve over different periods – for instance, three months, six months, a year, and three years. Having a vested interest in improving the metrics across the facility will give better results than an undefined efficiency goal.
How can Solvace help your business improve Operations in Manufacturing?
If your company wants to improve Operations in Manufacturing, Solvace professionals can help.
Solvace manages opportunities for improvement in manufacturing centered on visual management and problem solving using cutting-edge technologies.
Contact us and request a demo