Beyond connecting People, Processes and Technology within Manufacturing Industries: The AI era
Digitalizing the Operator Workplace
The manufacturing sector has undergone significant transformations since the inception of the first Industrial Revolution in the late 18th century. Driven by the development of steam-powered machines, this era marked the shift from manual labor to mechanized processes. As the world moved through successive industrial revolutions, the introduction of new technologies has continued to shape manufacturing, with the latest era, we call it the fourth industrial revolution, or Industry 4.0, characterized by the increasing digitalization and automation of processes. Digital transformation has become a cornerstone of modern manufacturing, and Industry 4.0 signifies the integration of advanced technologies such as the Internet of Things (IoT), artificial intelligence (AI), machine learning, and robotics into manufacturing processes. The operator workplace, a critical component of the manufacturing ecosystem, has not been left behind in this transition. That’s why both companies and governments like the European Union, are bringing Industry 4.0 to a 5.0 level, including people in this revolution that was until now dominated by predominantly a technological vision.
The primary drivers behind the shift towards digital transformation in manufacturing is the need for:
-
- Improved efficiency
- Standardized (global) quality
- Higher level of safety
- Increased Productivity
By digitalizing various aspects of the operator workplace, manufacturers can create a more connected and optimized system that leverages advanced technologies to streamline processes and enhance decision-making capabilities.
AI and automation play a pivotal role in the modern manufacturing landscape, offering numerous benefits such as reduced human error, improved quality control, and the ability to perform complex tasks with speed and precision. For instance, AI-powered predictive maintenance systems can analyze vast amounts of data from sensors installed on machinery to identify potential equipment failures before they occur, allowing for proactive intervention and reduced downtime. Until know (we talk 2023, when this article was written), knowledge was digitally stored and could be accessed, based on the users needs.
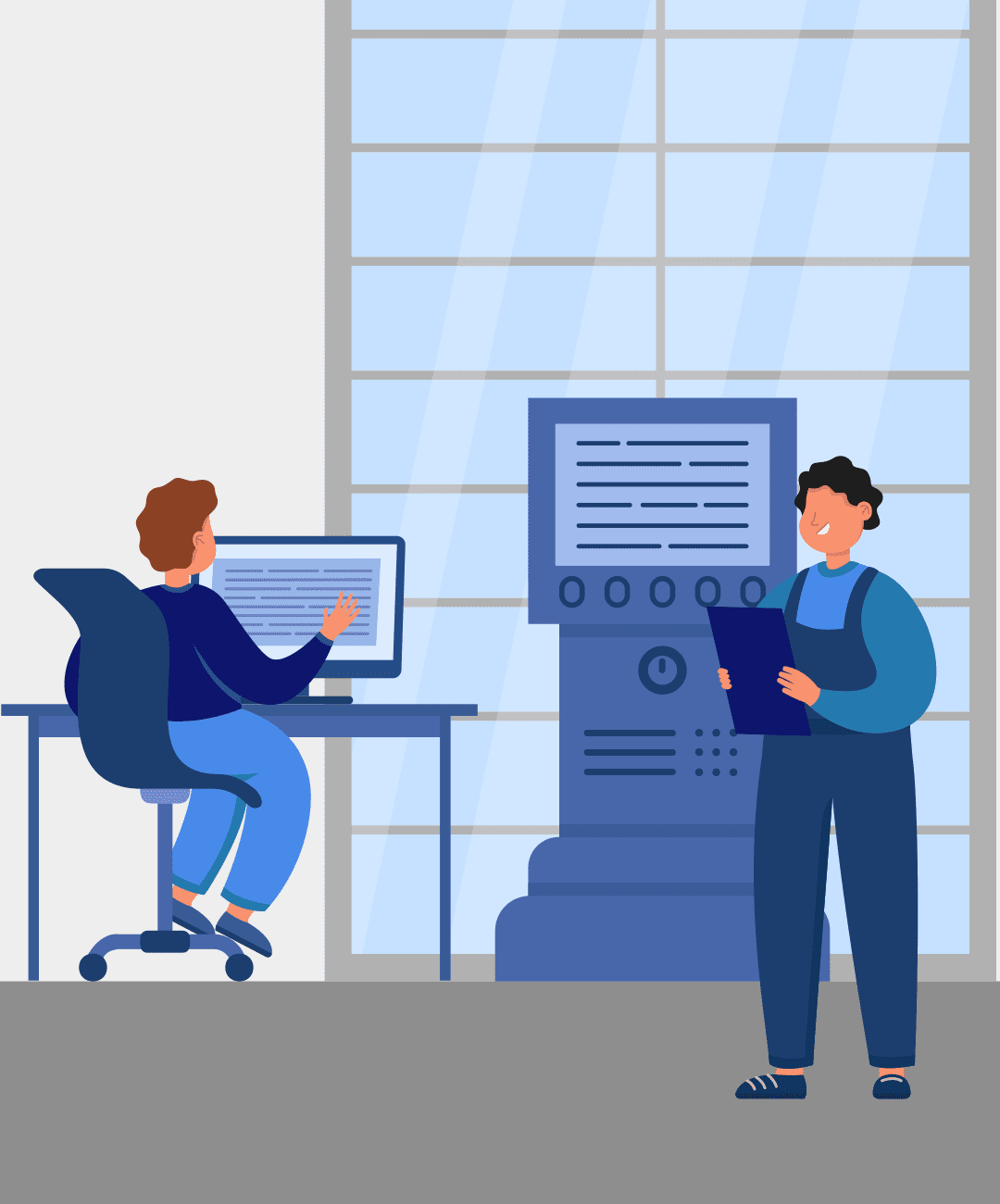
Today, with the use of AI, digital shopfloor platforms are able to generate proactively responses, that the operator might need by executing his or her tasks. A digital AI powered shopfloor platform, if connected to a manufacturing execution system (MES) can predict possible failures or increased (quality, safety) risks and push questions, solutions or warnings, even before a critical event takes place. This is in terms of Performance Behavior (Neil CW Webers, 2012) the (almost!) top level of performance management. The top excellence level will be the level when AI not only predicts a possible critical event, but also plans and executes all countermeasures to mitigate such a possible future event. Today, this is still the future. Humans are still a critical factor in the execution of tasks within a manufacturing environment. However, the most simple, heavy or unsafe tasks are step by step replaced by robots, which are more and more (partly) powered by AI systems, the integration of AI, automation or autonomization should for now not be seen as a complete replacement for human workers but rather as a complement to their skills and expertise. The most successful digital transformations will involve a careful balance between technology and human intervention, with both playing their part in driving excellence. To achieve this balance, it is essential to integrate people, processes, and technology within the manufacturing sector. This requires rethinking traditional approaches to workforce management and training, as well as fostering a culture that embraces innovation and collaboration. Manufacturers must invest in upskilling their employees to work alongside advanced technologies, enabling them to harness the full potential of digitalization in their day-to-day operations.
By digitalizing the operator workplace, manufacturers can also enhance communication and collaboration among employees, fostering a more connected work environment. The use of digital platforms and tools can facilitate real-time data sharing, allowing for faster decision-making and problem-solving. Moreover, advanced analytics capabilities can provide valuable insights into performance and process inefficiencies, enabling manufacturers to make data-driven decisions that drive continuous improvement.
Digitalization of the operator workplace within manufacturing is a crucial element in the ongoing transformation of the whole sector. By embracing advanced technologies such as AI and automation, manufacturers can create more efficient and connected systems that optimize processes, enhance decision-making capabilities, and ultimately drive operational excellence. However, the successful integration of these technologies requires a thoughtful approach to workforce management and training, ensuring that the human element remains a vital part of the manufacturing ecosystem. With the right balance between technology and human expertise, digitalization can pave the way for a more efficient, safe and sustainable future for the manufacturing industry.
Digitalizing Operational Excellence Processes within Manufacturing
Operational excellence is a widely-used improvement philosophy, in manufacturing that focuses on continuous improvement, waste elimination, and the pursuit of best practices in all areas of an organization. Examples are Total Productive Maintenance, Lean, Six Sigma and others. It is centered around enhancing the efficiency and effectiveness of processes while ensuring that products and services meet or exceed customer expectations. For manufacturers, achieving operational excellence is crucial for maintaining a competitive edge, increasing profitability, and driving sustainable growth.
In recent years, the role of digital technology in streamlining and optimizing operational excellence processes has become increasingly significant. Advanced technologies, such as artificial intelligence (AI), machine learning, and the Internet of Things (IoT), offer transformative capabilities that enable manufacturers to refine their processes, minimize waste, and drive continuous improvement. AI and machine learning, in particular, have the potential to revolutionize decision-making in manufacturing. By analyzing large volumes of data from various sources, such as sensors, production equipment, and quality control systems, these technologies can uncover hidden patterns and trends that may not be easily discernible through traditional analysis. This information can then be used to make data-driven decisions that improve production efficiency, reduce downtime, and optimize resource allocation.
Predictive maintenance is another area where AI and machine learning can have a significant impact on operational excellence. By leveraging historical and real-time data from equipment sensors, AI-powered algorithms can identify potential failures and maintenance issues before they become critical. This enables manufacturers to schedule proactive maintenance, reducing unplanned downtime, and minimizing the risk of costly equipment breakdowns.
Sales and Operations planning (S&OP) is another aspect of operational excellence that can benefit from the implementation of AI and machine learning. By analyzing data related to production schedules, inventory levels, and workforce capacity, these technologies can help manufacturers optimize their resources and improve overall operational efficiency. This may involve adjusting production schedules, reallocating personnel, or identifying opportunities to streamline the supply chain.
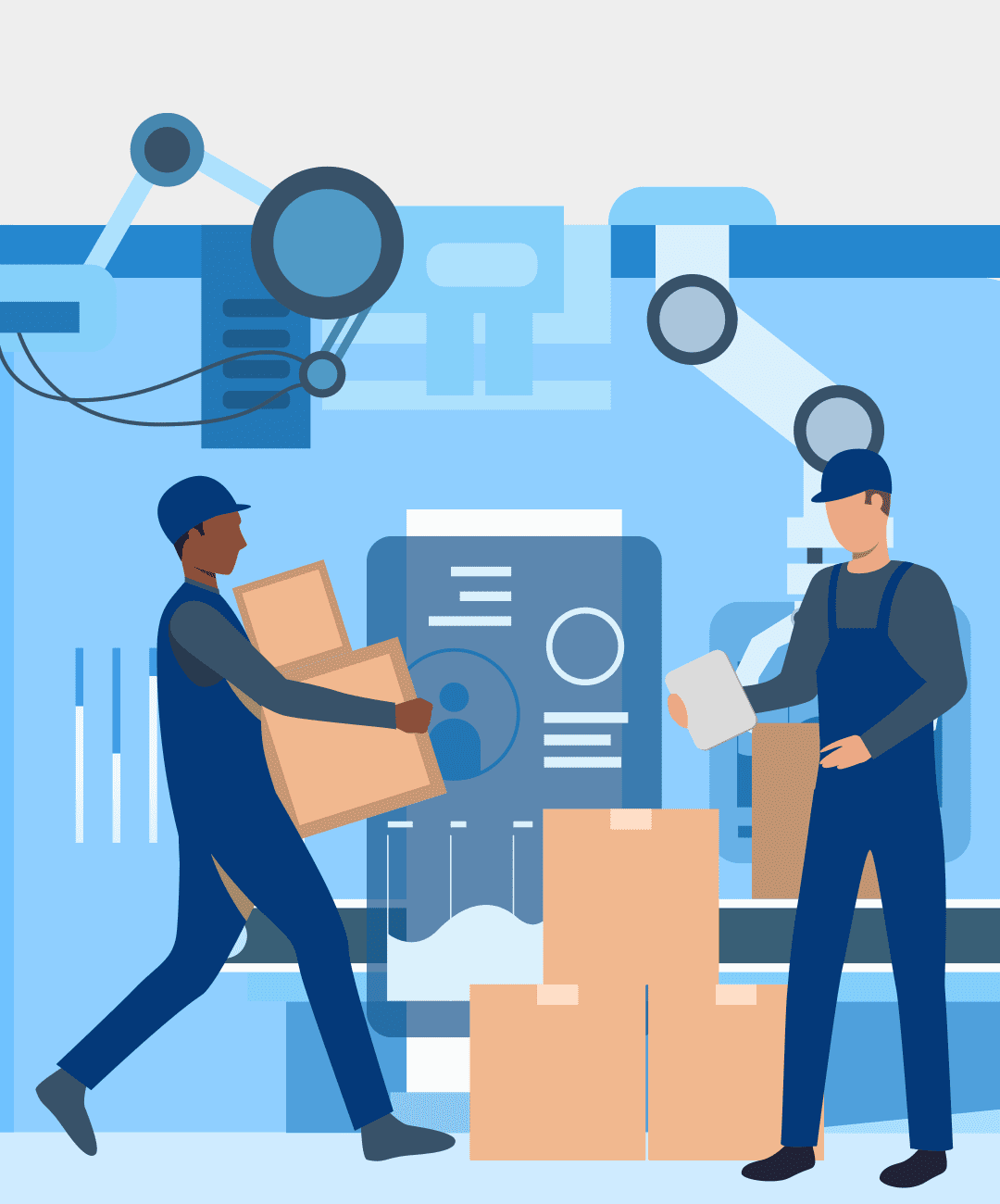
Today most manufacturing companies have successfully digitalized their operational excellence processes and achieved significant improvements. One example is Siemens, a multinational conglomerate that specializes in industrial automation and digitalization. By implementing AI-powered predictive maintenance solutions, Siemens has managed to reduce unplanned downtime and improve the overall efficiency of its manufacturing facilities. The company has also invested heavily in digital technologies such as IoT and machine learning, which have enabled it to optimize its processes and drive continuous improvement.
Another example is General Electric (GE), a global leader in manufacturing and technology. GE has embraced digitalization across its operations, using AI and machine learning to enhance decision-making, optimize maintenance schedules, and improve resource management. As a result, the company has reported significant improvements in efficiency, productivity, and overall operational excellence.
Digitalizing operational excellence processes in manufacturing is crucial for remaining competitive in today’s fast-paced, technology-driven world. By leveraging advanced technologies such as AI and machine learning, manufacturers can streamline their processes, improve decision-making, and optimize resource management. By learning from the successful implementation of digital solutions by industry leaders, companies can take steps to achieve operational excellence and drive sustainable growth in the digital era.
Revolutionizing Performance Management Processes within Food and Beverage Manufacturing
Performance management is a crucial aspect of manufacturing, encompassing the tracking, analysis, and optimization of operations to ensure that production processes are running efficiently and effectively. In the food and beverage industry, performance management is particularly important due to the need for stringent quality control, compliance with safety regulations, and the management of perishable goods. By digitalizing performance management processes, manufacturing companies in general and food and beverage manufacturers specifically can significantly enhance their operations and drive higher efficiency and productivity.
Digitalizing performance management processes involves leveraging advanced technologies, such as learning algorithms, artificial intelligence (AI), machine learning, and data analytics, to track and analyze operations in real-time. This allows manufacturers to identify inefficiencies, detect deviations from quality standards, and implement data-driven improvements. In turn, this can lead to increased productivity, reduced waste, and better overall performance. AI plays a critical role in digitalizing performance management processes by providing the capability to identify bottlenecks, predict trends, and make data-driven decisions. For example, AI-powered analytics tools can detect patterns and correlations in production data that may be indicative of bottlenecks or inefficiencies. By identifying these issues, manufacturers can take proactive steps to address them and improve their overall operational performance. AI-powered Performance Management platforms, such as market leader SOLVACE, suggests root causes and possible solutions, based on the users historic data and improvement topic that is used within the root cause analysis process. In this way, global improvement data does not need to be searched by the person, but is pro-actively pushed, so the person who is analyzing, can be more both more effective and efficient, solving the problem within his manufacturing domain.
AI can be used to predict trends and forecast future production needs, allowing manufacturers to optimize their resources and plan more effectively. This can be particularly beneficial in the food and beverage industry, where managing perishable goods and ensuring timely delivery to customers is essential. By leveraging AI for trend prediction, manufacturers can minimize spoilage, reduce waste, and better meet customer demand.
Several food and beverage manufacturing companies have successfully digitalized their performance management processes and achieved significant improvements in efficiency and productivity. One such example is PepsiCo, a leading multinational food and beverage corporation. PepsiCo has invested heavily in digital transformation, implementing advanced technologies like AI and data analytics to optimize their production processes and improve overall performance. By digitalizing their performance management processes, PepsiCo has been able to identify inefficiencies in their production lines, reduce downtime, and optimize resource allocation. With data and analytics approach, PepsiCo focusses on 4 key elements:
-
- Real-time updates on food to keep it fresh
Minutes matter as food travels to the shelves. Data can get it there faster and fresher by tracking where shipments are moment-by-moment and the temperature at which the food is being stored. PepsiCo is using unique Bluetooth-enabled sensors that can monitor the condition and pinpoint the location of any shipments.
-
- Brand innovation inspired by analytics
Gatorade is using data and analytics to optimize the way athletes exercise and the way PepsiCo develops new products. One of the most insightful tools is the Gatorade Gx Sweat Patch. After exercising while wearing the Sweat Patch, consumers upload their workout data to receive personalized recommendations for hydration and nutrition.
-
- Potato farmers developing more sustainable ways to grow
Farmers are an essential part of the company’s pep+ ambition to spread regenerative farming practices across 7 million acres by 2030. Now data is connecting farmers, providing a new path to meeting those goals. Farmers in Europe have gathered more than 1 million data points from over 118,000 acres of potato fields through PepsiCo’s iCrop technology. Data on soil type, weather, irrigation and water usage enable farmers to assess crop performance and develop practices to improve yields.
-
- Data upskilling programs for all associates
One of the company’s solutions is the Digital Academy. Through on-demand courses on topics including Data & Analytics, Cloud Technology, Machine Learning, and more, associates at all levels can start growing digital skills that apply to a wide range of roles. “
Another example is Nestlé, the world’s largest food and beverage company. Nestlé has embraced digital transformation across its operations, using advanced technologies like AI, machine learning, and data analytics to enhance its performance management processes. This has enabled the company to improve quality control, optimize production schedules, and better manage its extensive supply chain. Through the implementation of digital performance management solutions, Nestlé has reported significant improvements in efficiency, productivity, and overall operational performance. In one instance, the company used AI-powered analytics to optimize the production process of a beverage line, resulting in a 30% reduction in downtime and a 10% increase in overall line efficiency.
Digitalizing performance management processes is essential for manufacturing industry in general and for food and beverage manufacturers specifically, looking to optimize their operations and drive higher efficiency and productivity. By leveraging advanced technologies like AI and machine learning, companies can better track, analyze, and optimize their production processes, leading to significant improvements in performance. By learning from industry leaders like PepsiCo and Nestlé, food and beverage manufacturers can unlock the full potential of digital transformation and secure a competitive edge in the rapidly-evolving market landscape.
Transforming the Manufacturing Shop Floor in pharma and chemical companies
As mentioned in the first chapter, operators play a vital role in the manufacturing process, performing a range of tasks such as operating machinery, monitoring production lines, and ensuring quality and safety control. These key individuals within a manufacturing site are often the first to identify issues or inefficiencies on the shop floor, making their contributions essential to the overall success of a manufacturing operation. In recent years, digitalization has emerged as a powerful tool for enhancing the capabilities of shop floor operators, particularly in the chemical and pharmaceutical industries, where precision and efficiency are paramount.
Digitalizing operator tasks offers several key benefits, including improved communication, task automation, and real-time data analysis. By leveraging digital technologies, operators can more easily share information and collaborate with their colleagues, leading to faster problem-solving and decision-making. Digital tools can also help automate routine tasks, freeing up operators to focus on more complex or value-added activities. Furthermore, real-time data analysis can provide operators with valuable insights into the performance of the production process, enabling them to identify and address inefficiencies more effectively. AI and IoT technologies have the potential to significantly enhance operator decision-making, collaboration, and problem-solving on the manufacturing shop floor. For example, AI-powered analytics tools can analyze data from sensors and production equipment to detect anomalies or deviations from quality standards, alerting operators to potential issues before they become critical. IoT devices can enable real-time monitoring of production processes, providing operators with up-to-date information on the status of machinery and equipment.
In the chemical and pharmaceutical industries, several companies have successfully digitalized operator tasks on the shop floor, leading to increased efficiency and effectiveness. One company is Merck, a global pharmaceutical and chemical company. Merck has implemented a range of digital technologies, such as AI, IoT, and data analytics, to optimize its manufacturing operations and empower its shop floor operators. By digitalizing operator tasks, Merck has been able to improve communication and collaboration among its workforce, enabling faster problem-solving and decision-making. The company has also leveraged AI and IoT technologies to enhance real-time monitoring and data analysis, providing operators with valuable insights into the performance of their production processes. As a result, Merck has reported significant improvements in efficiency, productivity, and overall operational performance.
Another example is BASF, a leading chemical company that has embraced digital transformation across its operations. BASF has implemented digital technologies to streamline operator tasks, improve communication, and enable real-time data analysis on the shop floor. The company has also utilized AI and IoT solutions to enhance decision-making and problem-solving capabilities among its operators. Through the digitalization of operator tasks, BASF has achieved increased efficiency and effectiveness in its manufacturing operations. The company has reported improvements in productivity, reduced downtime, and better overall performance as a result of its digital transformation efforts.
Digitalization of operator tasks on the manufacturing shop floor is a powerful tool for enhancing efficiency and effectiveness, particularly in the chemical and pharmaceutical industries. By leveraging advanced technologies like AI and IoT, companies can empower their operators with improved communication, task automation, and real-time data analysis capabilities, leading to better decision-making and problem-solving. By learning from industry leaders like Merck and BASF, manufacturers can unlock the full potential of digital transformation and secure a competitive edge in the rapidly-evolving market landscape
Connecting Suppliers within a Digital Operational Excellence and Performance Management Platform
Supply chain management is a critical aspect of manufacturing, as it ensures the seamless flow of materials, components, and finished products between suppliers, manufacturers, and customers. As the manufacturing landscape becomes increasingly complex and globalized, the need for effective supply chain management is more significant than ever. A digital operational excellence and performance management platform can greatly enhance supply chain management by connecting suppliers and providing better visibility, collaboration, and agility. By connecting suppliers through digital platforms, manufacturers can gain several key benefits. One of the most significant advantages is improved visibility, as a digital platform allows manufacturers and suppliers to track and monitor the flow of materials and components in real-time. This ensures that both parties are aware of any potential issues or delays, enabling them to take proactive steps to mitigate risks and maintain the smooth operation of the supply chain.
Another major benefit of connecting suppliers through a digital platform is enhanced collaboration. By providing a centralized hub for communication and information exchange, digital platforms can facilitate better coordination between suppliers and manufacturers. This can lead to more efficient planning and execution of supply chain activities, as well as faster problem-solving and decision-making. Furthermore, digital platforms can foster greater agility in the supply chain, allowing manufacturers and suppliers to respond more effectively to changes in demand or disruptions in the supply chain.
AI technology can play a crucial role in optimizing supply chain management within a digital platform. By leveraging AI-powered analytics, manufacturers can improve supplier selection by identifying the best suppliers based on factors such as price, quality, and delivery performance. AI can also enhance demand forecasting by analyzing historical data and identifying patterns and trends, enabling more accurate predictions of future demand. This allows manufacturers to better align their production schedules and inventory levels with customer needs, minimizing the risk of stockouts or excess inventory.
One of the most effective ways to initiate such a digital platform initiative with suppliers is to focus on operational excellence, as both parties stand to benefit from the improvements in efficiency and effectiveness that it can bring. By collaborating on initiatives such as waste reduction, process optimization, and continuous improvement, manufacturers and suppliers can achieve tangible benefits that drive value for both parties.
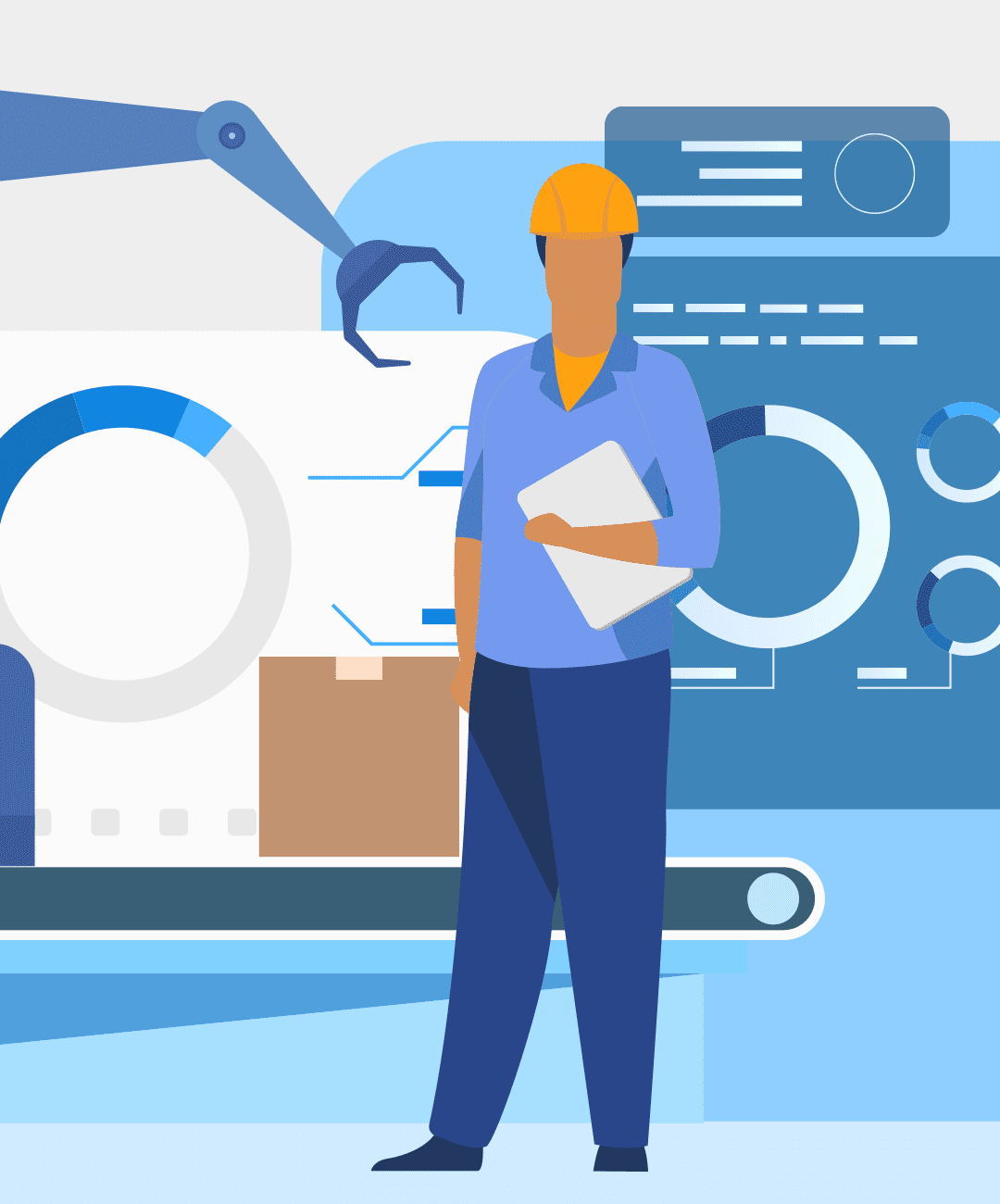
Several manufacturing companies have successfully connected their suppliers within a digital platform and experienced improved supply chain performance. For example, Procter & Gamble (P&G), a leading consumer goods manufacturer, has implemented a digital platform to enhance its supply chain management by connecting suppliers and streamlining communication and collaboration. By focusing on operational excellence initiatives with its suppliers, P&G has achieved significant improvements in efficiency, responsiveness, and overall supply chain performance.
BMW, a renowned automotive manufacturer also has embraced digital transformation across its supply chain. By connecting its suppliers within a digital platform, BMW has improved visibility, collaboration, and agility, enabling it to better manage the complex network of suppliers and partners that support its manufacturing operations. Leveraging AI technology, the company has also optimized supplier selection, demand forecasting, and inventory management, leading to increased efficiency and effectiveness in its supply chain. Now they take this a step further, combining 3D rendering with AI, partnering with NVIDIA, designing digital twins in full 3D, including people executing their tasks. The system enables BMW’s to see the real life effects on People, Processes and Technology in a 3D digital twin. This gives BMW the opportunity to take the right decisions based on the simulation data, before they implement it in real life.
Connecting suppliers within a digital operational excellence and performance management platform offers significant benefits for manufacturers, including improved visibility, collaboration, and agility in the supply chain. By leveraging AI technology, manufacturers can optimize various aspects of supply chain management, such as supplier selection, demand forecasting, and inventory management. By focusing on operational excellence initiatives with suppliers, both parties can achieve mutual benefits and drive value in their respective organizations. Manufacturing companies such as Procter & Gamble and BMW have demonstrated the power of digital platforms in enhancing supply chain performance, providing valuable insights for other manufacturers looking to embrace digital transformation in their supply chain operations
Conclusion
In this article, I have explored the impact of digital transformation on various aspects of the manufacturing industry, focusing on the integration of people, processes, and technology. By harnessing the power of AI, machine learning, and other advanced technologies, manufacturers can revolutionize their operations and drive increased efficiency, productivity, and overall performance.
The digitalization of the operator workplace enables manufacturers to streamline communication, automate routine tasks, and provide real-time data analysis for their shop floor operators. Companies such as PepsiCo and Nestlé have demonstrated the potential of digitalizing performance management processes, leading to significant improvements in efficiency, productivity, and overall operational performance. Digitalizing operational excellence processes within manufacturing allows companies to optimize their production lines and improve resource management. AI and machine learning can enhance decision-making, predictive maintenance, and resource management, as showcased by successful case studies from companies like Merck and BASF.
Connecting suppliers within a digital operational excellence and performance management platform can unlock the full potential of the supply chain, providing manufacturers with better visibility, collaboration, and agility. By focusing on operational excellence initiatives, manufacturers and suppliers can drive mutual benefits and improve overall supply chain performance, as demonstrated by companies such as Procter & Gamble and BMW.
Embracing digital transformation in the manufacturing industry is crucial for staying competitive in today’s rapidly evolving market landscape. By digitalizing various aspects of manufacturing operations, companies can create a more efficient, connected, and responsive system that maximizes the potential of people, processes, and technology. By learning from the successes of industry leaders and harnessing the power of AI, machine learning, and digital platforms, manufacturers can revolutionize their operations and secure a competitive edge for the future